Coordinating efforts to protect medical professionals
It’s been just over a month since the Sugiuchi household started using their 3D printers to create free face shields for medical workers on the front lines of the COVID-19 pandemic.
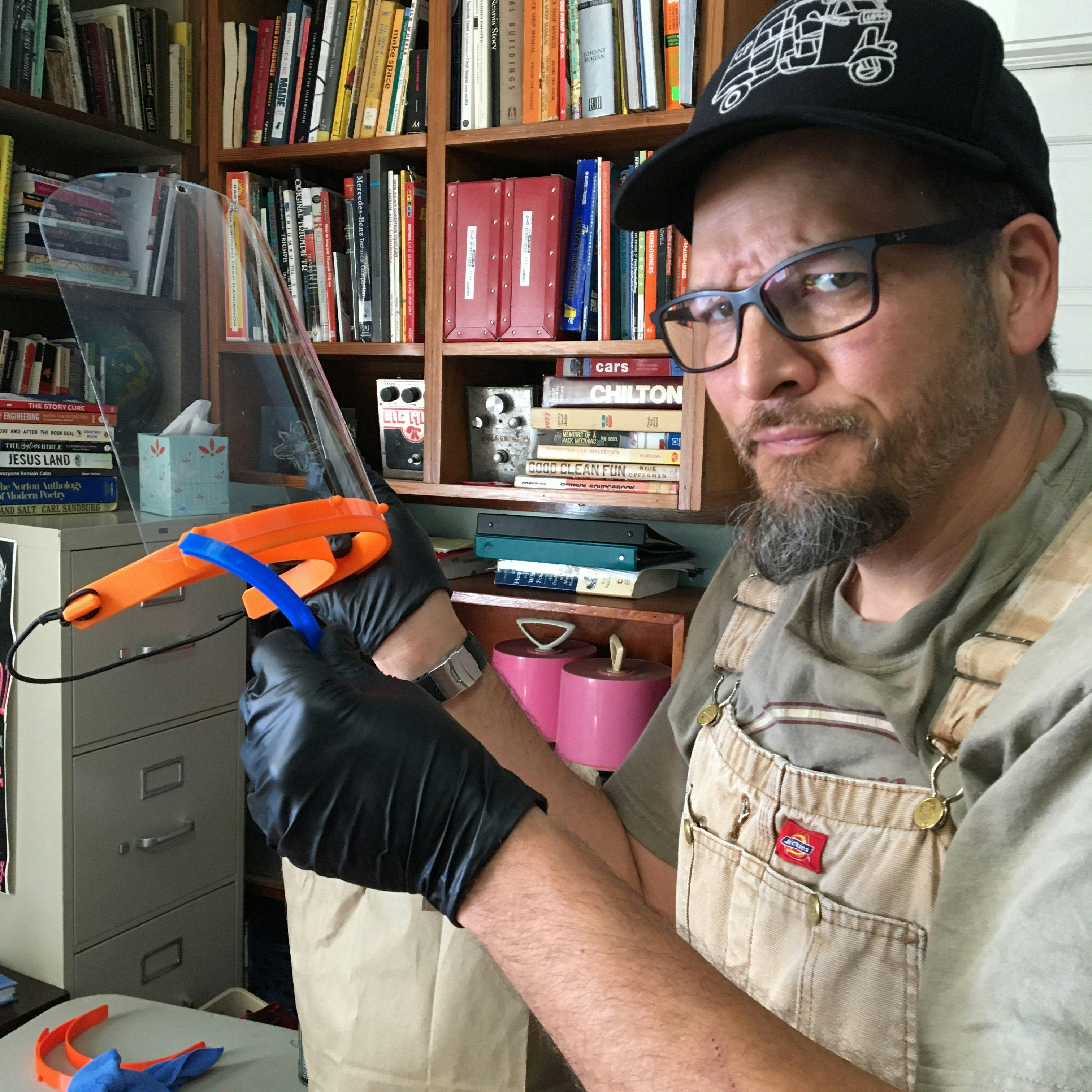
To date, Chris (B.S.Ed. ‘97, M.Ed. ‘01) and Deirdre (M.Ed. ‘01) Sugiuchi, both alumni of the UGA Mary Frances Early College of Education, have created over 1,800 face shields for dozens of hospitals, clinics, health centers and organizations in Georgia, including the police department in Watkinsville.
“We had no idea we would still be making face shields at this point,” said Deirdre, who received her master’s degree in instructional technology and her specialist degree in English education. “Just the other day, we got an email from a surgery center in Athens. They had ordered face shields commercially, but they didn’t come in. So, that’s the type of thing that healthcare professionals are having to deal with.”
Before the outbreak, Chris, who serves as a STEM teacher at Chase Street Elementary School, casually grabbed the 3D printer in his classroom to learn more about the machine during spring break. However, when his school closed, the Sugiuchis found themselves in a unique position to help combat shortages of personal protective equipment (PPE) in Georgia.
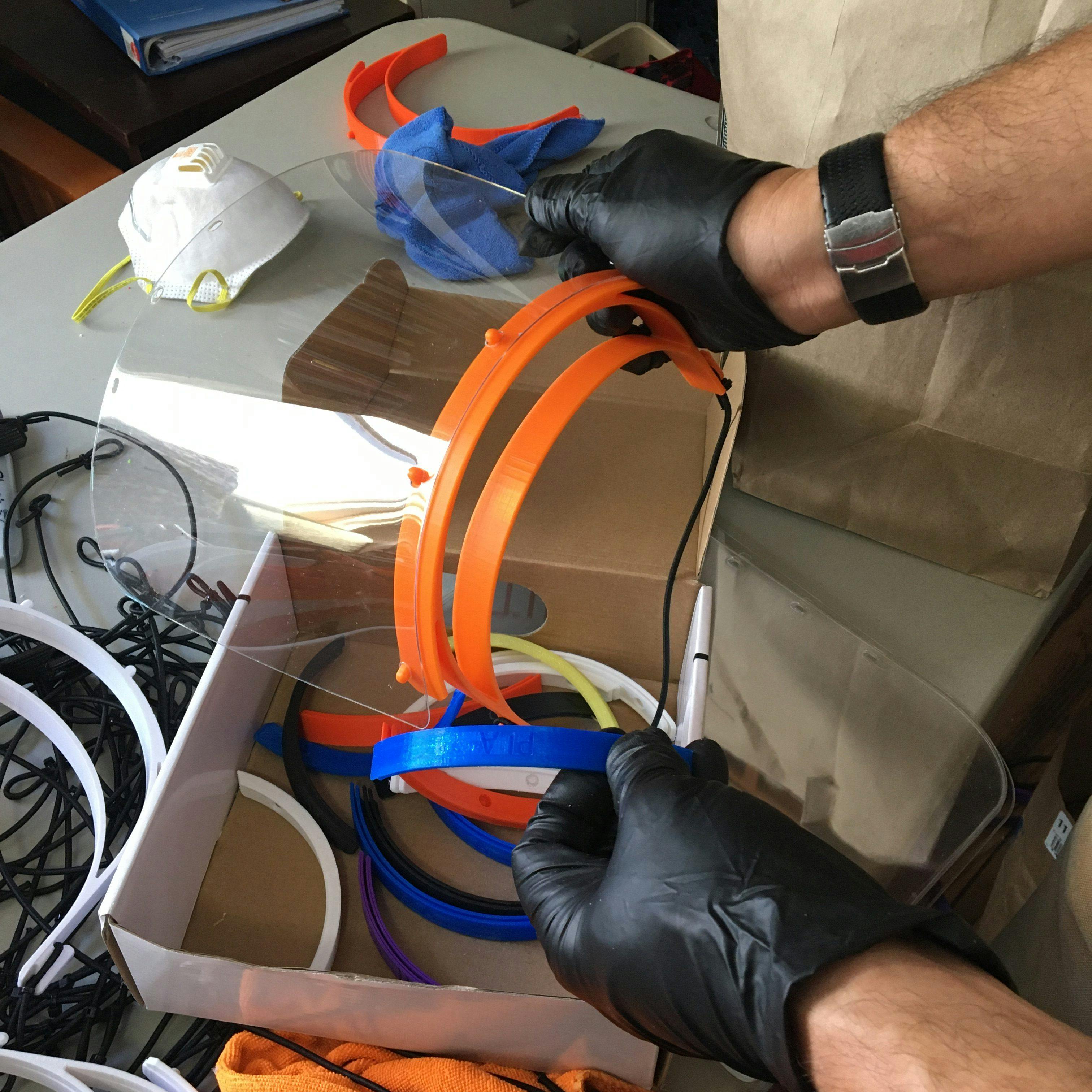
After reading about how people in Italy were using 3D printers to make pieces for ventilators, Chris and Deirdre decided to download a face shield design from PrusaPrinters—an open-source website based in the Czech Republic with 3D printer designs—so they could create PPEs and help medical professionals like Deirdre’s sister, a nurse in Asheville, North Carolina, combat COVID-19.
“Prusa were the ones who came up with the original design, and then we iterated the design and came up with the style we’re using now,” said Chris, who received both his bachelor’s and master’s degrees in technology education. “We have two laser cutters to cut the clear part of the face shield, and we are 3D printing the mounting bracket, which we call the headband.”
Chris collaborated with his neighbor Dr. Karl Barnett, who works in the Piedmont Athens Emergency Medicine Department, on the first face shield prototype. A month later, Barnett and many of his coworkers in the emergency room are still using these face shields, which can be sterilized and reused numerous times in conjunction with cloth masks or N95 respirator masks.
After making hundreds of face shields for institutions ranging from Piedmont Athens Regional Medical Center and St. Mary’s Hospital to the Athens Alliance Coalition and Athens Housing Authority, Chris and Deirdre have nearly perfected the face shield-making process—from printing the headbands, laser cutting the shield component from PETG plastic (the same kind used to make water bottles) and then mounting the headband using an elastic strap. Since the buttonhole elastics used in the original design are sold out, they are now using a bungee cord-like material, which connect the two components of the shield. Throughout the process, they have acquired a greater appreciation for medical and health professionals.
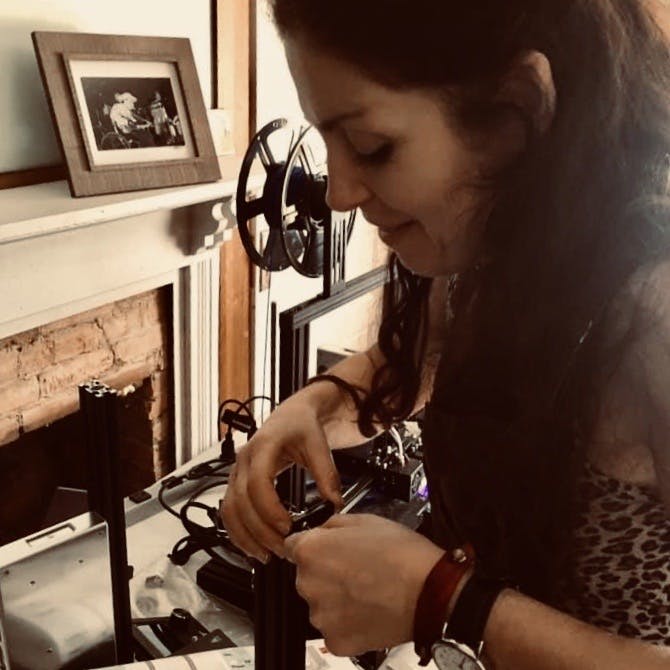
“Hope Haven is sending caregivers into the homes of developmentally disabled adults who are being cared for by their elderly parents,” said Chris. “You think about people with severe Down syndrome and the caregivers who have to go into their homes, and it’s sometimes very difficult for those people to comprehend why this person who usually greets them with a hug are not able to do that anymore, and it’s just really challenging. There are groups of professionals like that where I think, ‘Oh, I didn’t even imagine all the situations where people need to have PPE.’”
Overall, it takes approximately four hours to create one face shield from start to finish, but by printing around the clock, the Sugiuchis can produce about 50 face shields per day. Thanks to donations from their neighbors, community members, and University units like the Lamar Dodd School of Art, the two have been able to continue their PPE-making efforts by purchasing more printers (they currently have nine) and materials.
The pair started Shield Athens, a project consisting of other people in the community who have 3D printers and are collaborating on making headbands for shields, finding materials, fundraising and designing more PPEs. After the pandemic ends, Chris plans on bringing the printers back to his school, so his students can use them to create STEM projects.
3D printing in the College
William Immonen (M.Ed. ‘16), an IT professional specialist in the Mary Frances College of Education’s Office of Information Technology (OIT), recently joined Athens’ informal “makers” group and has been working closely with faculty and staff in both the College of Education and the College of Engineering to produce headbands for face shields, with the support of Dean Denise A. Spangler and Lloyd Rieber, professor and head of the department of career and information studies (CIS).
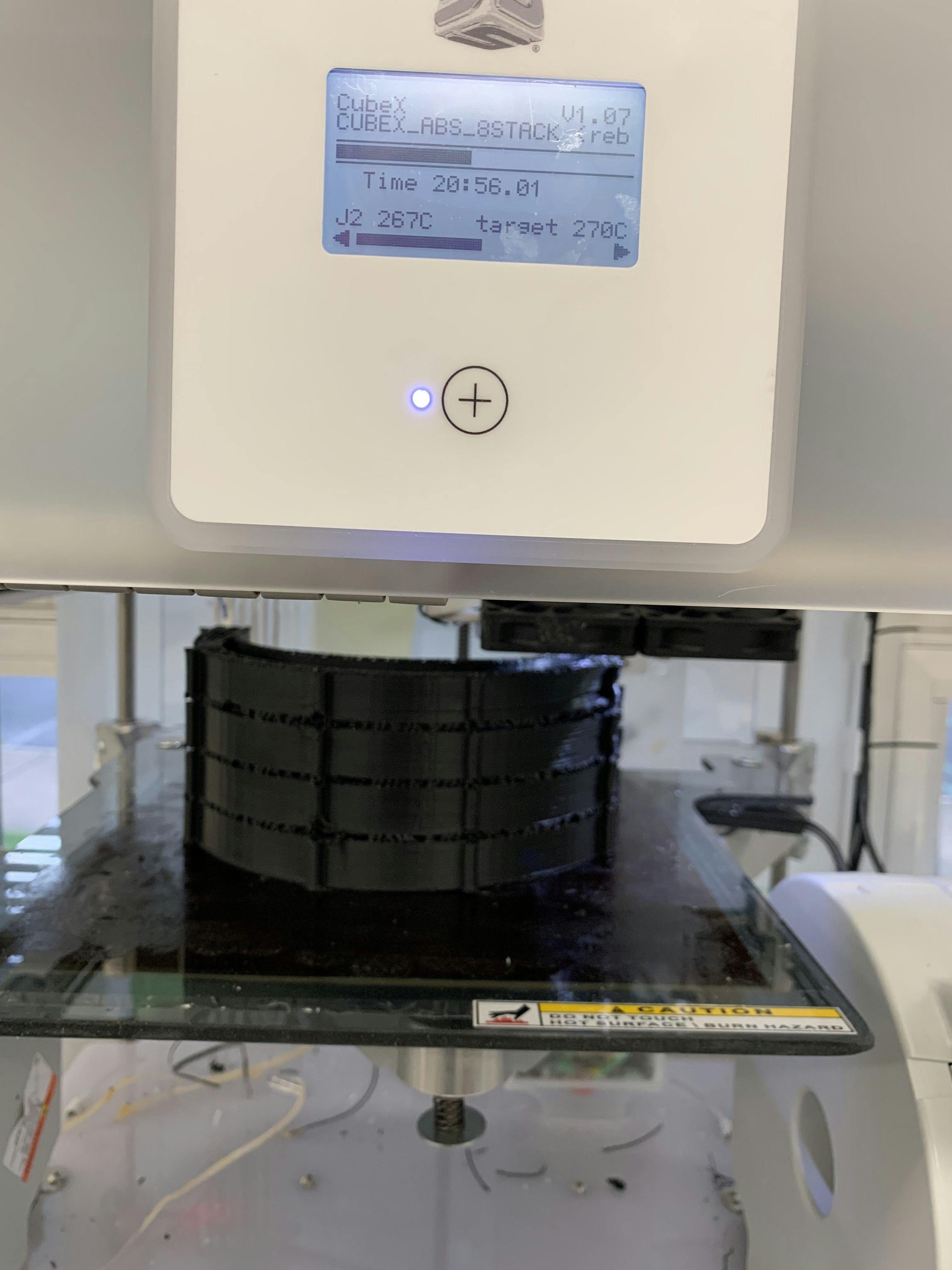
“Drs. Nancy Knapp and Janette Hill contacted me asking what we could do to help, and I told them it depends on what our goals are, and how much work we’re willing to put into the project,” said Immonen, who graduated from the College’s learning, design and technology program and is currently pursuing a master’s degree in business and technology from Terry College. “I had a call with Drs. Rob Branch in the College and Roger Hilten from engineering, and we saw where the College could help, what engineering was doing currently and what they were planning for in the future.”
While only one out of the nine printers in CIS is big enough to produce the headbands, Immonen began running several tests in River’s Crossing after receiving approval. These tests allowed him to assess whether the College’s 7-year-old 3D printers could be a viable option. Since early April, he has produced a total of eight headbands using a plastic-like material called acrylonitrile butadiene styrene (ABS), which took around 40 hours to print.
Although he is only capable of producing the headband component of the face shield, Immonen can contribute to UGA’s overall effort of producing PPEs by dropping his 3D-printed pieces off at the University’s Instrument Design and Fabrication Shop, where several units, including the College of Engineering and UGA Libraries are collaborating to create face shields for local medical professionals.
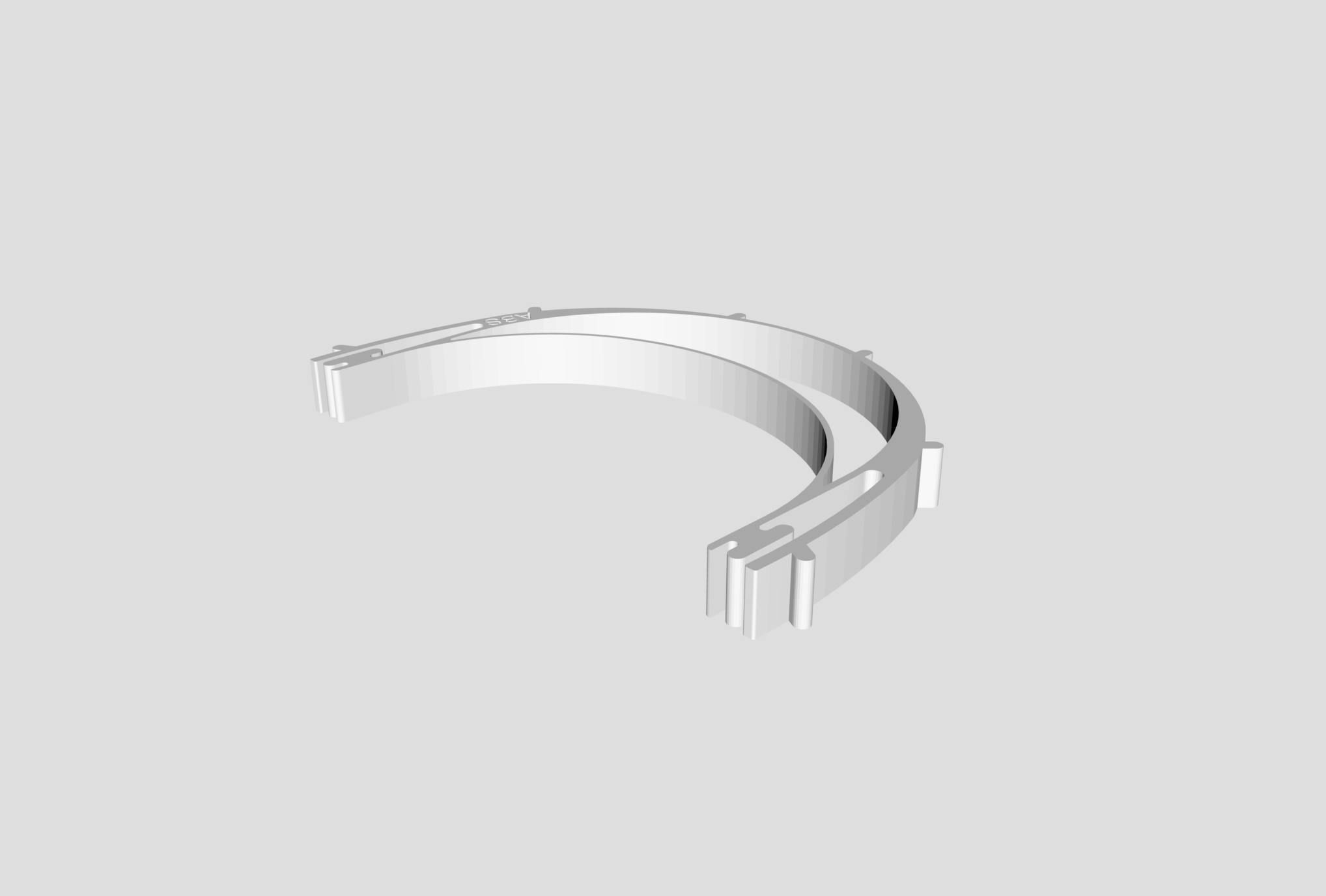
“We create the headbands that hold the clear plastic shields,” he said. “Engineering and fabrication have water jet cutters, so they are able to make the shields out of the correct materials. All of this is a coordinated effort.”
Unfortunately, the department’s 3D printer broke a couple weeks ago during the middle of a print job. However, Immonen is actively searching for a solution to fix the machine, so he can start producing more headbands for the College of Engineering as they continue to donate more face shields to St. Mary’s Health Care System and Piedmont Athens Regional.
“I want to thank Dean Spangler and all the administrators that okayed this to make sure we’re following the legal paths to keep UGA and everyone else safe,” said Immonen. “Since I work for OIT, I don’t actually own the resources for the 3D printing, so I always ask to use them. They’ve given me a lot of leeway, and I’m trying to make sure everything’s okay with them.”